The right foundation for long-lasting floors
It’s what’s underneath that counts
Long-lasting success is usually based on a sound foundation. Just like athletes start by building up their endurance and their muscles, also house construction starts with laying the foundation. The same applies to the substrate: Careful substrate preparation is the foundation of successful flooring installation. Failure to do so may result in later damage to the floor. Repair work is not only time-consuming but also expensive.
A major issue in many homes is the replacement of old floor coverings. The musty carpet needs to be removed and the outdated ceramic tiles must give way to high-quality parquet, trendy luxury vinyl flooring or modern large-format tiles. The first thing to do is to completely remove the old floor covering – including any adhesive residues. Before installing the new flooring, the substrate must be carefully checked. A few simple criteria can help.
The key factor for achieving good results is an absolutely even substrate. If the screed does not have a level surface, flooring materials like parquet or laminate may later break if there is a hollow space underneath. Carpets and vinyl or PVC flooring are able to adapt to unevenness, but the resulting bumps are not a pretty sight – and can even pose a tripping hazard. In general, it is advisable to firmly bond the flooring over the entire surface. This makes it more robust, hard-wearing and durable. A level substrate ensures that there is a firm and reliable bond between flooring and substrate. It also reduces impact sound and enables effective heat transfer from the underfloor heating system. If, however, the substrate has cracks, holes or other defects, a levelling compound or filler is necessary to provide a surface of uniform evenness.
Just as important is the strength of the substrate. Otherwise, there will be a risk of adhesive failure. The easiest way to determine the strength is the so-called grid scratch test. A pointed metal object (e.g. a nail) is used to scratch a rhombus (#) into the substrate. If there is no flaking along the edges or where the scratch lines cross, the subfloor is of sufficient strength.
When planning the installation of floors in a newly built house, special attention must be paid to the floor moisture. In new-builds, the residual screed moisture is often underestimated. If the screed is not sufficiently dry, its moisture not only impairs the adhesion of the flooring adhesive but, in the worst case, also promotes the development of mold and odor. New screeds are not always ready to receive flooring after four weeks – this is just the lower time limit. How quickly the screed dries strongly depends on factors such as air humidity, ambient temperature and thickness of the screed slab. It is therefore highly recommended to have the substrate preparation done by a professional floorer. If you prefer to lay the floor yourself, you should at least ask an expert to check the residual screed moisture. Before bonding the new floor covering on top of the expertly prepared subfloor, it must be carefully cleaned. Make sure to sweep or vacuum the surface so that no remaining dust or dirt particles can impair adhesion.
To ensure your indoor climate is unpolluted and free from harmful substances emitted by adhesives, levelling compounds or primers, it is advisable to employ building and installation products that have been certified with the EMICODE® label. These products are only awarded the EC1 seal if they meet the most stringent emission limits. Their compliance with the limit values is monitored by experts from independent laboratories and testing institutes. Thus, building owners can be sure to enjoy a sustainable and healthy home.
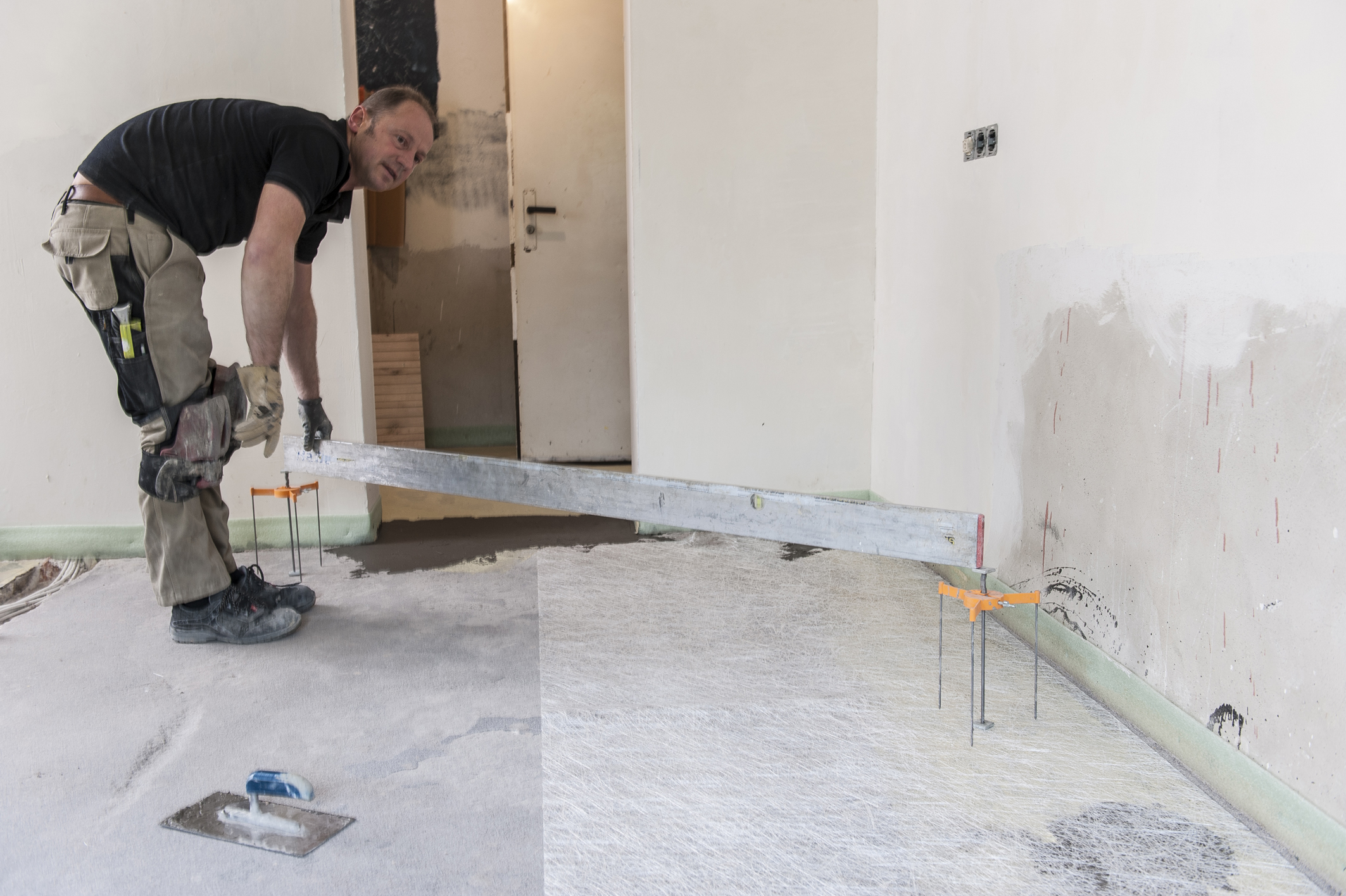
Photo: GEV
A level subfloor is key: Without proper substrate preparation, there will later be a high risk of damage and costly repairs for your newly installed floor covering. Laminate, for example, can break on uneven surfaces or hollow areas. Wooden materials like parquet can swell if the residual screed moisture is too high. And vinyl or PVC flooring may form bumps or waves. It is therefore advisable to have a professional floorer prepare the subfloor so that it is sound, even, dry and clean. To ensure maximum indoor health, the building and installation materials used should carry the EMICODE® quality seal.
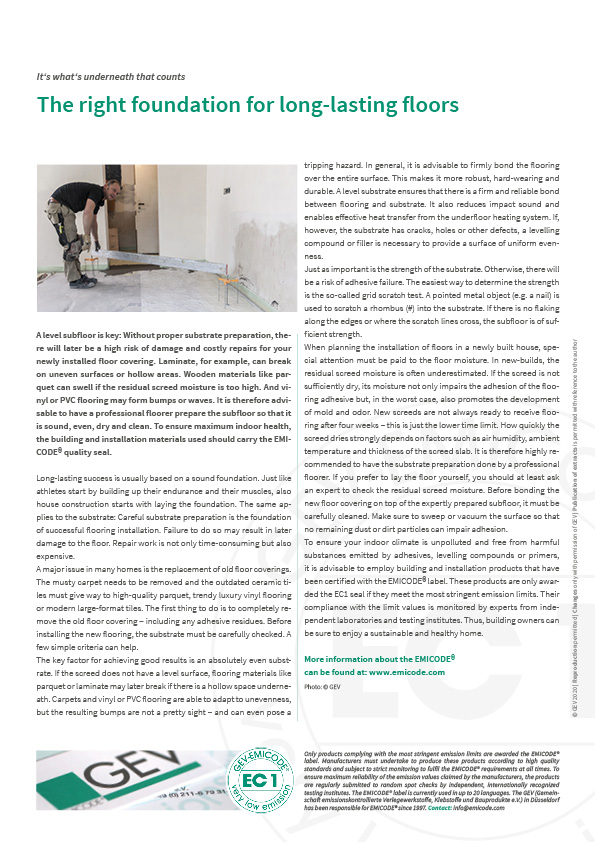
Do You Have Questions?
If you have questions about specific topics or if you would like to contact us for any other reason, feel free to contact us by phone, fax or e‑mail.
Phone: +49 211 / 67931–20
Fax: +49 211 / 67931–33
info@emicode.com
Share article on Social Media: